The benefits of dry ice blasting for every industry and the role of compressed air
Author: Alex Persyn, Director of Product Management ROTAIR Portable Compressors
In the dynamic world of manufacturing and production, maintaining equipment efficiency and cleanliness is paramount. Traditional cleaning methods often fall short in meeting the rigorous standards and precision required in sectors like food and beverage, pharmaceuticals, automotive, electronics and more. This is where dry ice blasting, also known as CO2 blasting, comes into play.
According to a recent market analysis, the "Dry Ice Blasting & Cleaning Equipment Market" is poised for significant growth from 2023 to 2030. This surge is attributed to increasing demands in various sectors, including general industry, food & beverage, automotive and others. And there are many good reasons behind that.
Basics of dry ice blasting technology
Dry ice blasting, an advanced cleaning technique in industrial settings, incorporates a unique interplay of kinetic energy, thermal shock and sublimation for optimal cleaning efficacy. When dry ice pellets are propelled at high velocity, they impart kinetic energy to surface contaminants. Upon impact, the extreme cold temperature of the dry ice induces a thermal shock effect, causing brittleness and cracking in the residue. This effect is particularly effective for removing stubborn deposits, like grease, oil and biofilm, without damaging the underlying surface.
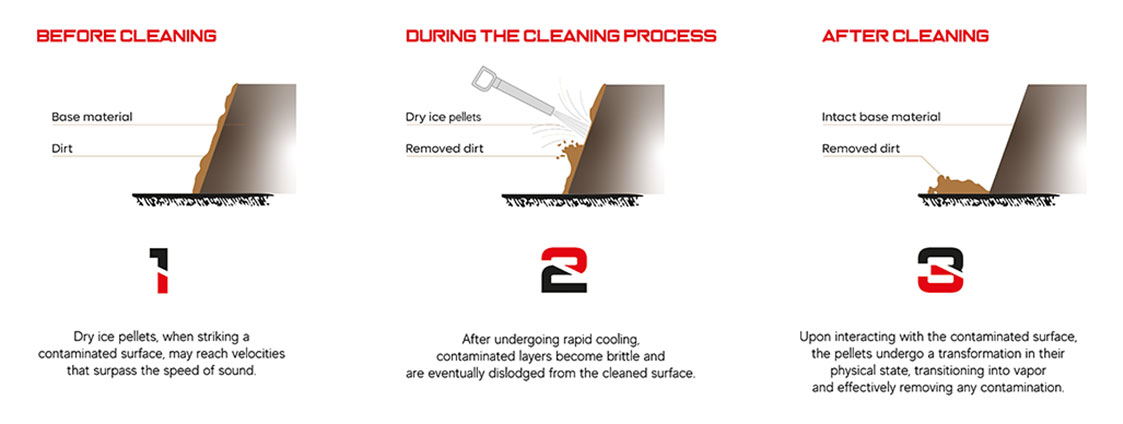
The sublimation aspect of dry ice – its transition from solid to gas without passing through a liquid phase – is pivotal in this process. As the dry ice pellets strike the surface, they sublime instantly, expanding rapidly to dislodge and lift dirt and debris. This unique property ensures that no secondary waste is produced, distinguishing dry ice blasting from traditional methods like sandblasting or water-based cleaning, which often leave residual materials.
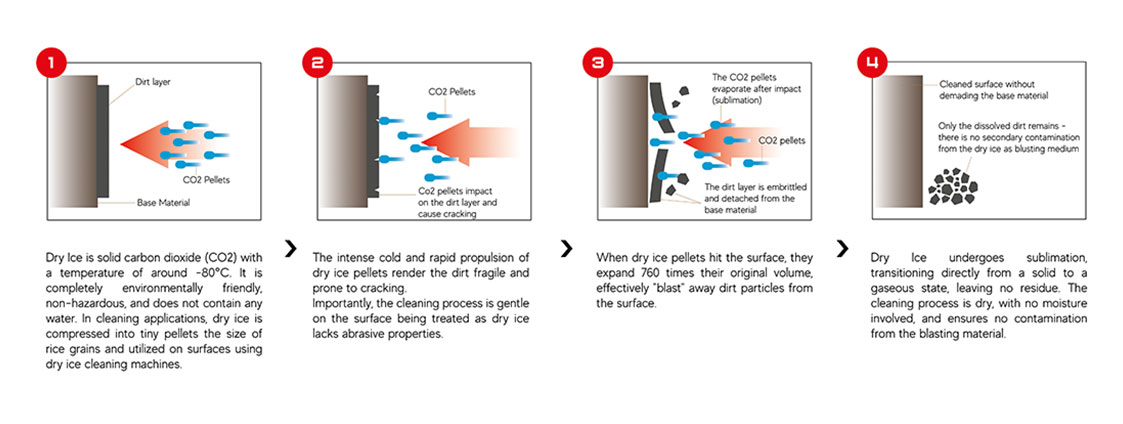
Advantages of dry ice blasting
This gentle yet efficient technique allows for the cleaning of various surfaces, including metal, wood, concrete, glass, textiles, or electronics without dismantling objects, machines and equipment. This saves both time and money.
Additionally, dry ice is effective in inhibiting bacterial growth and reducing fungi, spores and other biological contaminants. Its non-toxic, odourless nature makes it suitable for diverse applications, ensuring a clean and sanitary environment.
The advantages of dry ice blasting are numerous and diverse, making it a preferred cleaning method across various industries:
- Non-Abrasive : Safely cleans delicate surfaces without damage.
- Environmentally Friendly : Utilizes reclaimed CO2, producing no secondary waste and is non-toxic, non-conductive, and non-flammable.
- No Chemical Residue : Leaves surfaces free of chemical contaminants, ideal for the food, pharmaceutical and electronics sectors.
- Waterless Cleaning : Avoids water-related damage, perfect for "electrical" components and sensitive machinery.
- Reduced Downtime : Offers a quick and efficient cleaning process, minimizing operational interruptions.
- No Disassembly Required : Cleans equipment in situ, saving time and labour.
- Versatile Use : Effectively removes various contaminants (like grease, oil, paint, adhesives) from different surfaces, including industrial machinery and delicate historical artifacts.
Better for business and the planet
Dry ice blasting offers a multifaceted approach to industrial cleaning that is both environmentally-friendly and effective. A key aspect of its environmental advantage is the sourcing of dry ice itself; it is derived from reclaimed CO2, a by-product of other industrial activities. This process does not generate additional CO2 emissions, thus having a neutral impact on the greenhouse effect. What is more, dry ice blasting reduces the environmental footprint by replacing harmful detergents and solvents. This shift not only contributes to a healthier planet but also reduces the exposure of employees to hazardous chemicals, thereby minimizing corporate liability and enhancing workplace safety.
The role of compressed air
The air compressor is a key component in dry ice blasting systems. Its ability to deliver the right volume and pressure of air is essential for the optimal performance of the blasting process, making it a vital factor in achieving efficient, effective, dry and safe cleaning results.
Determining the air volume requirements for dry ice blasting is crucial for optimal performance and depends largely on the specific application and the type of dry ice blasting machine used. The range of cleaning pressures in dry ice blasting applications is quite broad, spanning from as low as 1 bar to as high as 15 bar. This versatility allows dry ice blasting to be tailored to a wide array of cleaning tasks, from delicate surfaces needing lower pressure to more robust applications that demand higher pressure. The flexibility in adjusting both the air volume and pressure makes dry ice blasting a suitable method for diverse industrial cleaning needs, ensuring both efficacy and safety for various types of surfaces and materials.
Additionally, in cases where lower air volumes and pressures are required, a versatile compressor with adjustable settings becomes crucial. This flexibility allows operators to fine-tune the blasting process according to the specific requirements of the task, ensuring both safety and effectiveness.
The right air quality
In dry ice blasting systems, the quality of compressed air is paramount, with specific requirements in terms of pressure, flow, and dryness. Compressed air naturally contains water vapor, which can condense and cause issues in the dry ice blasting equipment. To address this challenge, an Aftercooler can be used to cool down the hot air from the compressor, maintaining the dryness and integrity of the dry ice. The Aftercooler also includes a water separator that traps moisture, thus ensuring that the air used in the blasting process is sufficiently dry. This system is crucial for maintaining the temperature differential essential for effective dry ice blasting. Adapting air compressors to meet the specific requirements of dry ice blasting is a critical aspect of ensuring the efficiency and effectiveness of this cleaning technology. Leading air compressor manufacturers recognize this need and are adapting their machines accordingly. For instance, Rotair's VRK model and similar machines are being designed to cater specifically to the unique needs of dry ice blasting, focusing on providing the right quality and volume of air.
This adaptation involves modifications to ensure that the compressors not only deliver air at the correct pressure and volume but also ensure that the compressed air is as free from oil and moisture as possible. Moisture in contact with dry ice will freeze and may cause problems at several levels. For example, Rotair’s VRK+ features a unique onboard integrated dual-stage aftercooling system. Other compressor models in the range can also be equipped with an onboard aftercooler.
Generally, for manual or intermittent dry ice blasting projects, a compressor with an aftercooler and low parts per million (ppm) will suffice. For specific or automated applications, a second aftercooler and even additional fine filtration could be provided.
Here are some specific ways in which dry ice blasting is making a significant impact:
Top-Tier Hygiene Standard for Food and Beverage Industry
In the food and beverage industry, compliance with hygiene standards is of utmost importance and any lapse in protocol can lead to significant health risks and production delays. Dry ice blasting is now considered the "gold standard" cleaning medium in the food and beverage industry, noted for its effectiveness and safety. The dry ice used is a food grade media enabling the cleaning of entire areas without the need for chemicals and long drying times as ice evaporates directly into gas.
In the food and beverage industry, dry ice blasting can effectively clean a variety of equipment, including industrial ovens, wafer oven plates, air conveyor systems, conveyors and mixers, adhesives used in packaging, conveyor belts, bottle fillers, labellers, and coffee roaster equipment.
Pioneering Safety in the Automotive Industry
Dry ice blasting is rapidly becoming the go-to solution in automotive sector, celebrated for its precision, safety and non-abrasive nature that is ideal for the delicate and intricate components of automotive machinery. It effectively removes tough contaminants like oil, grease and dirt from critical components without the use of additional chemicals nor blasting abrasives, ensuring the longevity and reliability of vehicles.
Dry ice blasting is particularly effective for:
- Deep Cleaning of Metal Parts : Thoroughly cleans engine components, chassis, wheel rims and other metal surfaces without the risk of damage.
- Gentle Care for Rubber Components : Safely and efficiently cleans rubber parts including hoses, seals and gaskets, preserving their integrity and functionality.
- Electronic Components Maintenance : Ensures maximum safety and efficacy in cleaning various electronic components, crucial for modern vehicles.
- Sensitive Sensor Cleaning : Offers a safe and effective solution for cleaning delicate sensors, crucial for vehicle performance and safety.
- Interior Detailing : Expertly cleans textiles and plastics within the vehicle’s interior, including seats, floor mats, dashboards, ensuring a pristine environment.
- Dry ice blasting in the automotive industry not only upholds high cleanliness standards but also contributes to the overall health and safety of the automotive manufacturing and maintenance process. With its ability to clean effectively without leaving any residues, dry ice blasting is an indispensable tool in the automotive industry, aligning perfectly with the sector's need for precision, safety and environmental responsibility.
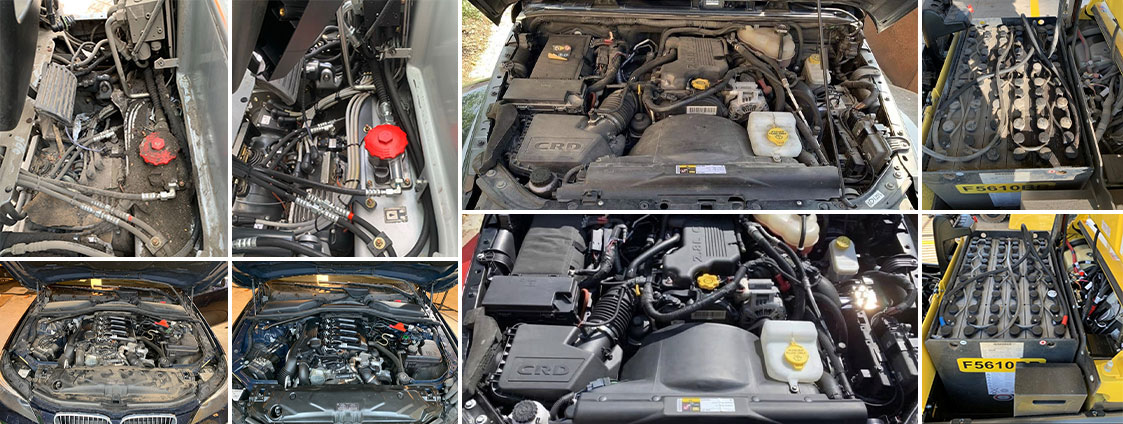
Integrating Abrasive Blasting and Dry Ice Blasting for Optimal Surface Preparation
In the evolving landscape of surface cleaning and preparation, it is crucial to recognize the unique strengths and applications of both abrasive blasting and dry ice blasting. Abrasive blasting has long been a cornerstone in the industry, especially valued by key accounts such as efficient removal of heavy rust, thick paint layers, or stubborn corrosion. Its aggressive nature makes it an ideal choice for tackling demanding cleaning tasks.
However, the introduction of dry ice blasting into the market has opened new avenues for precision cleaning. This method, while gentler than abrasive blasting, excels in scenarios where a delicate and dry touch is required. It is particularly effective in preserving the integrity of the underlying substrate, ensuring that the cleaning process does not inadvertently damage the material.
The synergy of these two techniques can be harnessed for a comprehensive cleaning strategy. By initially employing abrasive blasting for the heavy-duty removal of coatings and contaminants, and subsequently utilizing dry ice blasting for a precise, residue-free finish, it's possible to achieve a thorough and meticulous cleaning result. This tandem approach not only ensures an optimal cleaning outcome but also minimizes potential damage and waste, demonstrating the complementary nature of these two methods in the field of surface preparation and cleaning.
Conclusions
As we continue to witness advancements in industrial processes, the adoption of innovative cleaning technologies like dry ice blasting is becoming increasingly essential. Its unique ability to deliver thorough cleaning without causing damage or leaving behind harmful residues makes it an invaluable tool across diverse industries, including manufacturing, food and beverage and automotive. Moreover, its alignment with environmentally-friendly practices, through the use of reclaimed CO2 and the absence of secondary waste, underscores its role in promoting sustainability. Alongside the long-established technique of abrasive blasting, which effectively handles heavy-duty tasks, dry ice blasting offers a complementary, precision-focused approach. Together, these methods can address a broad spectrum of cleaning challenges.
In recognizing the integral role of air compressors in this process, it's crucial to emphasize the importance of collaborating with air compressor manufacturers that offer solutions tailored specifically to dry ice blasting. These manufacturers, acknowledging the advantages of this application, support and offer machines suitable and adaptable to enable effective dry ice blasting. Without the right air compressors, capable of delivering the necessary air volume and quality, dry ice blasting, as a cutting-edge cleaning solution, wouldn't be possible. The compressed air industry should be providing the best technology and support, turning itself into active enablers and those that can improve the effectiveness and quality of the process.